Machinery is the backbone of modern society, powering everything from transportation to manufacturing. The smooth functioning of these complex machines relies on various components working together seamlessly.
An element that is often forgotten, yet crucial for ensuring machinery reliability is the use of seals. These seemingly simple devices are sure to prevent leakage and contamination, which can lead to equipment failures and costly downtime. Keep reading to explore the role of seals in maintaining machinery reliability.
Types of Seals
Seals come in various types, each designed to serve different purposes. Here are some common seal types used in machinery:
- O-rings: These round, rubber seal rings are typically used in hydraulic and pneumatic systems.
- Lip seals: Also known as oil seals, these are used to prevent lubricant from leaking out of bearings or gearboxes.
- Mechanical seals: These are used to prevent leaks in pumps or other rotating equipment by using two flat faces pressed together with a fluid barrier in between.
- Gaskets: These are flat seals used to prevent leaks between two stationary parts, such as flanges or covers.
- V-ring seals: These are used in dynamic applications where there is movement in the shaft, such as rotating shafts or cylinders.
Look for the Right Manufacturers
When seeking to enhance machinery reliability through the use of high-quality seals, it’s critical to partner with reputable manufacturers. Expertise in seal design and material selection is paramount, as these factors play a significant role in the seal’s effectiveness and durability. In terms of gaskets, look for UK gasket manufacturers, for instance, known for their quality and expertise in producing gaskets that can withstand extreme temperatures, corrosive substances, and high pressures. Choosing the right manufacturer guarantees the reliability of the seals while contributing significantly to the overall efficiency and longevity of the machinery.
The Science Behind Seal Design
Have you ever wondered how seals are designed to function in various applications? Seal design is an intricate process. The science behind it takes into account several factors such as the type of fluid, pressure, temperature, and desired level of leakage. On top of that, the material of the seal is carefully considered as it will determine the seal’s strength, durability, and resistance to wear and tear.
The engineering process is a blend of theoretical calculations and practical testing to ensure the seals meet the desired specifications. The results of these efforts are seals that are reliable, efficient, and cost-effective in their application, from medical equipment to agricultural machinery. A thorough understanding of the science behind seal design ensures the longevity and reliability of machinery.
Factors Affecting Seal Performance
While seals maintain machinery reliability, several external factors can affect their performance. These include exposure to extreme temperatures, corrosive substances, and wear and tear due to friction. Routine maintenance and regular inspection of seals are necessary to identify any potential issues before they escalate into costly downtime or equipment failure.
Temperature Fluctuations
Temperature fluctuations can cause seal materials to expand or contract, resulting in a loss of sealing ability. Thermal cycling can also cause material fatigue and premature failure. Selecting the right material for the specific operating temperature range is crucial to avoid these issues.
Chemical Exposure
Seals that come into contact with harsh chemicals need to be made from materials resistant to corrosion and degradation. If not, the seals can weaken and lose their ability to effectively prevent leakage.
Friction and Wear
Seals in dynamic applications are constantly moving and rubbing against other surfaces, causing friction and wear. Eventually, this can lead to seal failure. The right material selection, as well as proper lubrication and maintenance, can extend the lifespan of seals in these applications.
Maintenance Tips for Long-lasting Seals
To ensure the continued reliability of seals in machinery, here are some useful maintenance tips to keep in mind:
- Regularly inspect and replace worn or damaged seals.
- Use the correct lubricants and ensure proper lubrication levels.
- Keep seals clean to avoid contamination.
- Monitor temperature and pressure changes that may affect seal performance.
- Partner with reliable manufacturers for high-quality replacements.
- Invest in preventative maintenance to catch any potential issues before they escalate.
- Train employees on proper seal installation and maintenance techniques.
Case Studies
To further demonstrate the critical role of seals in maintaining machinery reliability, here are some real-life case studies:
- A manufacturing plant experienced frequent downtime due to equipment failures. After consulting with a seal manufacturer and switching to high-performance seals, they saw a significant decrease in downtime and production costs.
- An agricultural equipment company noticed increased wear on their machinery due to dirt and debris entering the seals. By implementing proper seal maintenance and investing in improved sealing solutions, they were able to extend the lifespan of their equipment and reduce maintenance costs.
- A medical device manufacturer was experiencing product contamination due to leaking seals. After working with a trusted seal supplier and using specialized seals designed for their specific application, they were able to eliminate contamination issues and improve product quality.
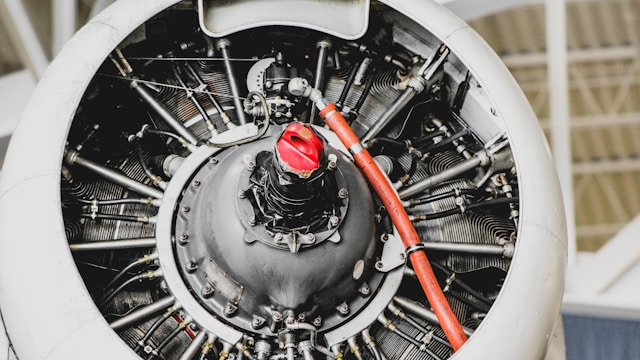
The seemingly simple component of seals holds a paramount role in the reliability and efficiency of machinery across various industries. From manufacturing plants to medical devices, the right seal can drastically reduce downtime, extend equipment lifespan, and save costs. Organizations can ensure their machinery operates at peak performance.